Stuart Ablett
Member
- Messages
- 15,917
- Location
- Tokyo Japan
We had a good day today, I found out that there is a Viva Home center (not Super Viva Home) fairly close to my house, only 12Km away, took less than 30 minutes from my parking to the parking at the store, that is a LOT closer than the Super Viva Home I usually go to. It is a smaller store, thus they have less stuff, but they still have a LOT more stuff than anything that close. 
I got the new angle iron, and did some work on the Back Bench after we got my SIL moved into her new Aparto.
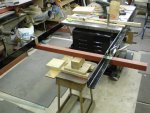
I took the front tube and the extension table off to work on the support brackets, here you can see the angle iron in place.
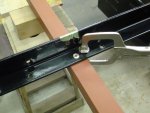
I drilled and counter sunk a hole for the bolt to go into, worked slick!
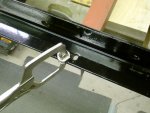
On the front rail, I made an oblong hole, just like the rails has in it, so the fence tube can be adjusted front to back. The fence tube bolt will hold this end in place.

On the left side of the saw, I drilled and counter sunk holes for the bolts, again, it worked well.
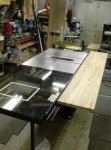
I put the two slabs in place (they are NOT yet laminated together) to see how things line up, fairly good I'd say!
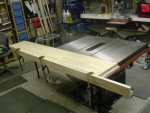
I then put the apron in place, held with clamps. The apron is just long enough for what I want to do, the over hang on the apron will be filled in with another double slab. I purposely left a step in the two slabs, to make the joint between the slabs coming at 90 degrees stronger...............
Cont.......

I got the new angle iron, and did some work on the Back Bench after we got my SIL moved into her new Aparto.

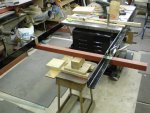
I took the front tube and the extension table off to work on the support brackets, here you can see the angle iron in place.
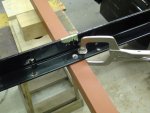
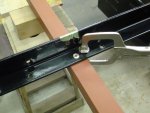
I drilled and counter sunk a hole for the bolt to go into, worked slick!
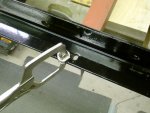
On the front rail, I made an oblong hole, just like the rails has in it, so the fence tube can be adjusted front to back. The fence tube bolt will hold this end in place.
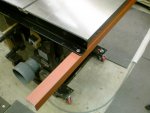

On the left side of the saw, I drilled and counter sunk holes for the bolts, again, it worked well.
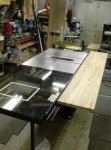
I put the two slabs in place (they are NOT yet laminated together) to see how things line up, fairly good I'd say!
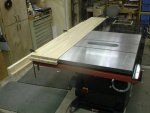
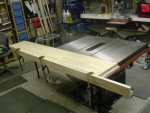
I then put the apron in place, held with clamps. The apron is just long enough for what I want to do, the over hang on the apron will be filled in with another double slab. I purposely left a step in the two slabs, to make the joint between the slabs coming at 90 degrees stronger...............
Cont.......