Mark Patrick
Member
- Messages
- 108
- Location
- Loxahatchee,Fl
This has been a long process I will start with saying that. When I bought this house 10 years ago the plans were to build a shop for "my toys". The deal with "she who must be obeyed" was that she got a pool and tile thruout the house and I got my shop. Fast forward to September 13th of 2020, I finally got the cash together to pay for the building. We signed the contract on that day and we were off. I am glad I signed when I did as very shortly they would update pricing to almost double .
We broke ground in October only to get our first issue. The survey company came out to core sample the corners of the building pad. Well 3 out of 4 were perfect and the 4th they stated was a disturbed area and would need to be excavated. They stated there is no way that what they hit 5 foot down was cap rock ( common in this area) and it needed to be dug up.
I got a small hoe rented and started to excavate the corner. At 5 feet I pulled up with a little help a 5.5 foot long 4 foot wide and almost 2 foot thick piece of Limestone cap rock. The core drill hold damn near dead center. The engineer had argued with me that it can't be cap rock as my lot was an old pineapple farm. I politely sent him photos of the rock with the core drill markings and told him he could feel free to say he was wrong at any time.
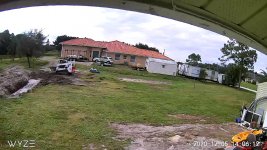
With the go ahead from the engineer and survey crew we started to bring in fill. In total it took 46 trucks of fill.
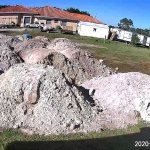
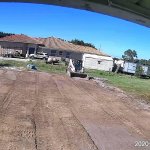
We got it compacted and formed up for concrete, had it termite treated and had the compaction density tests done.
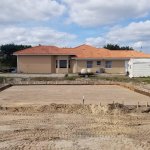
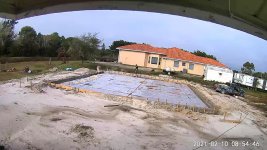
Pour day came on a Saturday morning, crews were here at 5am and trucks quickly started arriving
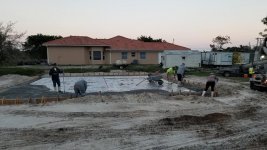
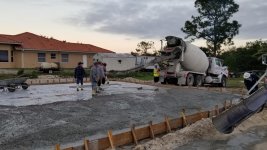
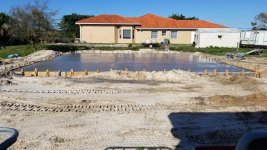
We broke ground in October only to get our first issue. The survey company came out to core sample the corners of the building pad. Well 3 out of 4 were perfect and the 4th they stated was a disturbed area and would need to be excavated. They stated there is no way that what they hit 5 foot down was cap rock ( common in this area) and it needed to be dug up.
I got a small hoe rented and started to excavate the corner. At 5 feet I pulled up with a little help a 5.5 foot long 4 foot wide and almost 2 foot thick piece of Limestone cap rock. The core drill hold damn near dead center. The engineer had argued with me that it can't be cap rock as my lot was an old pineapple farm. I politely sent him photos of the rock with the core drill markings and told him he could feel free to say he was wrong at any time.
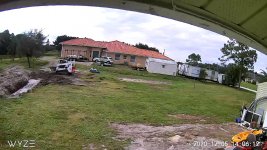
With the go ahead from the engineer and survey crew we started to bring in fill. In total it took 46 trucks of fill.
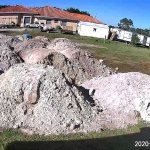
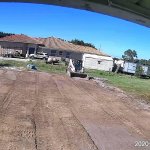
We got it compacted and formed up for concrete, had it termite treated and had the compaction density tests done.
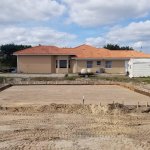
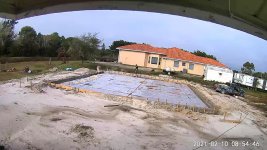
Pour day came on a Saturday morning, crews were here at 5am and trucks quickly started arriving
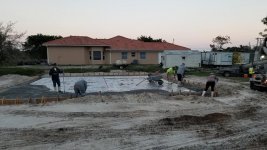
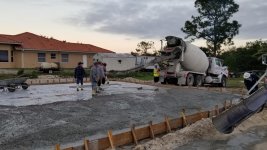
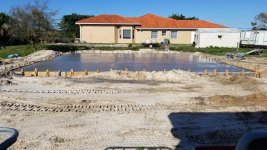