Continuing to work through the tops. I face joint those boards that are 8" or less. Ya gotta love those long infeed tables.
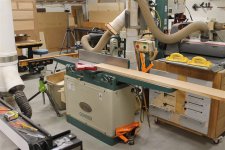
For wider boards one remembers that ANY extra material only adds to the deviation from flat and square that we are after.
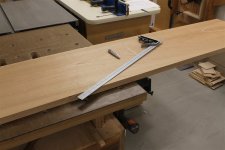
I remove any waste that I know will be removed anyway.
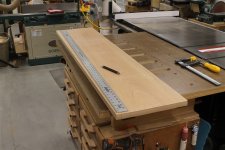
This is done at the abdnsaw for rip cuts.
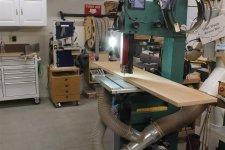
Plenty of kindling for the marshmallow toasting evenings.
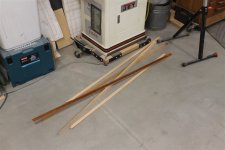
cordless jig saw does duty as a cutoff saw.
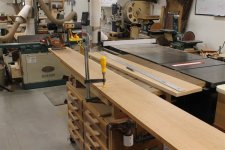
I have had an issue with the planer hose for some time. I finally decided now is the time to deal with it.
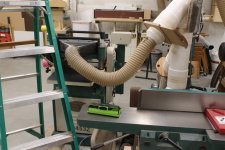
I use a plumb bob to find the location in the ceiling that will serve my purposes.
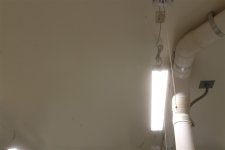
Since there is no stud close enough to serve me I will use the leftover hardware from hanging the DC duct work.
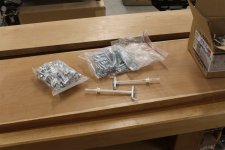
Since this connecting point will have a bit of swing to it I want a goo, large bearing surface for the drywall. I'm going with this. I do not remember what the bell shaped washer was from but I am glad I have it in the "misc" box.
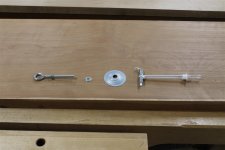
The Strong Tie toggle connector goes through a 1/2" hole into the ceiling drywall.
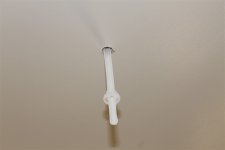
You slide the collar up and snap off the feeder bar.
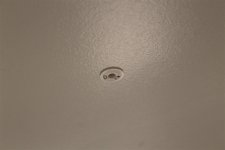
The 1/4" x 20 screw eye feeds in and washers and a nut take care of torquing things down. Care is take here as you do not want the eye to twist but, you are anchoring to a sandwich press in drywall.
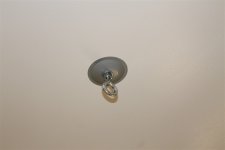
This lets me hold the hose out of the way when required (which isn't often).
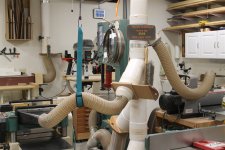
When not in use it is just a bungee hanging from the ceiling.
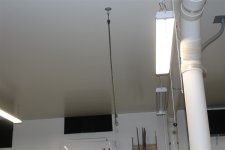
This is just a repeat of the planer sled use previously shown.
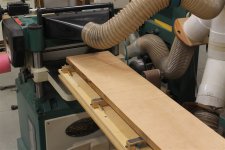
I will use the drum sander to finish off the dimensioning while prep'ing the surface for later.
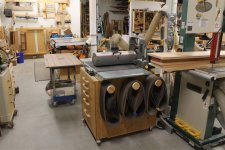
I use one of the bandsaws as a supply surface for the drum sander.
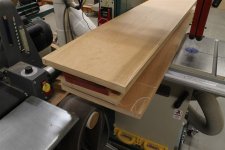
And a cart as the exit support platform.
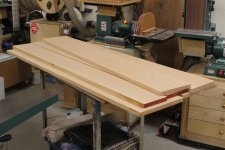
I layout the rough-width but near-final-thickness parts to double check figure and color matching.
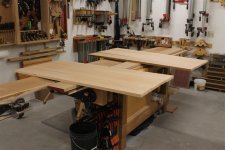
Good thing I did since I mixed up some part orders . . .
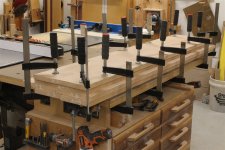
My back is screaming at me so I will just let these rest and come back tomorrow to final width and glue up the tops.