glenn bradley
Member
- Messages
- 11,565
- Location
- SoCal
These are part of the bedroom "collection" that started with the Blanket Chest several months ago. I will take my time on these since I would like to finish them up about the time the remodel of the room where they will go gets done. Ah . . . the best laid plans
. There will be a pair of them and this is the general thing I am shooting for.
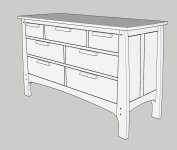
As always it starts with material selection. I had used up much of my 4/4 cherry on other projects over the last couple of years and was surprised when I didn't have enough stock I liked when I went to start this project!?! Off to the local yard for some stock for the drawer fronts and end panels.
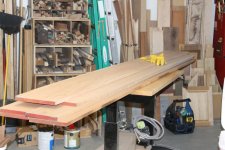
I made this leg template over a year ago. Common story . . . I never knew it would take this long to get started on the remodel. At any rate, I use it to layout leg blanks on some thicker stock.
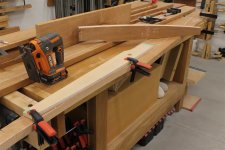
I cut the blanks to length with the jig saw and bandsaw the basic shapes out. I then joint one face and plane to thickness. The extra block of scrap is milled along with the parts to give me something at dimension in case I need to test anything later.
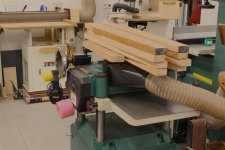
Since I will be doing a fair amount of 1-1/8" tall template routing I do a touch up on the bit I plan to use. Remove the bearings and give each face 2-3 swipes of fine and extra fine.
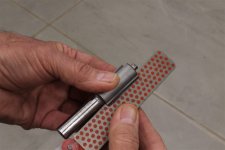
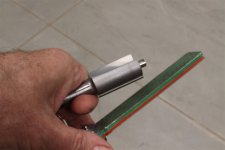
I use the same Template Jig I made back in 2011. It seems to cover most of my template routing needs and hasn't required a rebuild yet
.
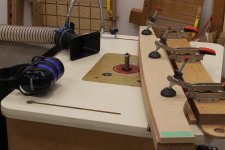
Here's a tip many of you may already use on burn prone woods. Run a piece of tape along the template edge and make your cut.
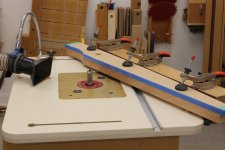
Pull the tape and make a second pass. This often gives you nice, clean, burn-free edges even in difficult materials.
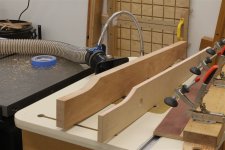
This is with both faces and the long edges done. Ready to crosscut to length.
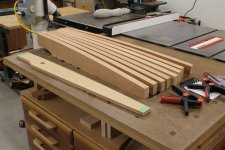
One thing about template routing is that it can generate a lot of spoil no matter how close you bandsaw to the line. My router table catches a lot of the spoil but in these types of operations a lot of spoil flies off the cutter well above the throat collection area. As you can see in the previous pics I add a vac collection point on top of the table. The little man in my head tells me I should check the vac collection tub. I loosen the little green wing doo-jobber on the 4" hose.
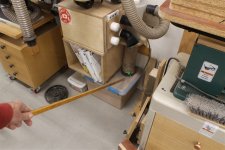
This lets me slide the tub out.
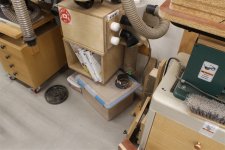
Yep, that needs to be emptied.

In contrast here is the filter box showing how much spoil gets past the Dust Deputy . . . almost none.
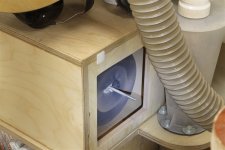
I use the same router template like a story stick to set the cross cut location at the top of the leg. I then just use a stop block to set the overall length.
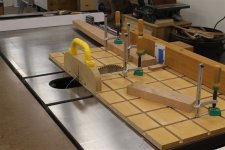
And I end up here.

On to the other parts that make up the end panels.
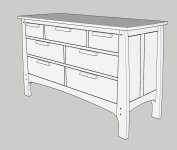
As always it starts with material selection. I had used up much of my 4/4 cherry on other projects over the last couple of years and was surprised when I didn't have enough stock I liked when I went to start this project!?! Off to the local yard for some stock for the drawer fronts and end panels.
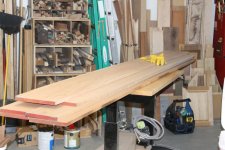
I made this leg template over a year ago. Common story . . . I never knew it would take this long to get started on the remodel. At any rate, I use it to layout leg blanks on some thicker stock.
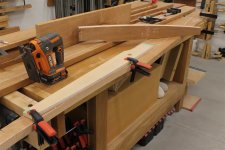
I cut the blanks to length with the jig saw and bandsaw the basic shapes out. I then joint one face and plane to thickness. The extra block of scrap is milled along with the parts to give me something at dimension in case I need to test anything later.
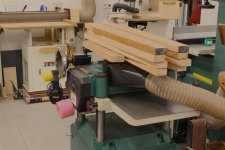
Since I will be doing a fair amount of 1-1/8" tall template routing I do a touch up on the bit I plan to use. Remove the bearings and give each face 2-3 swipes of fine and extra fine.
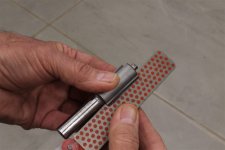
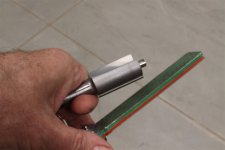
I use the same Template Jig I made back in 2011. It seems to cover most of my template routing needs and hasn't required a rebuild yet
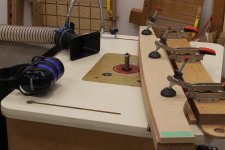
Here's a tip many of you may already use on burn prone woods. Run a piece of tape along the template edge and make your cut.
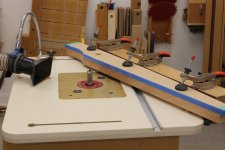
Pull the tape and make a second pass. This often gives you nice, clean, burn-free edges even in difficult materials.
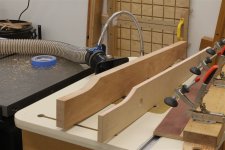
This is with both faces and the long edges done. Ready to crosscut to length.
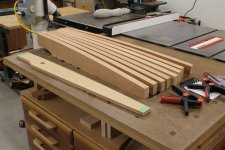
One thing about template routing is that it can generate a lot of spoil no matter how close you bandsaw to the line. My router table catches a lot of the spoil but in these types of operations a lot of spoil flies off the cutter well above the throat collection area. As you can see in the previous pics I add a vac collection point on top of the table. The little man in my head tells me I should check the vac collection tub. I loosen the little green wing doo-jobber on the 4" hose.
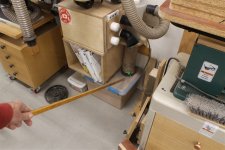
This lets me slide the tub out.
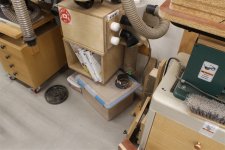
Yep, that needs to be emptied.

In contrast here is the filter box showing how much spoil gets past the Dust Deputy . . . almost none.
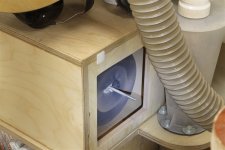
I use the same router template like a story stick to set the cross cut location at the top of the leg. I then just use a stop block to set the overall length.
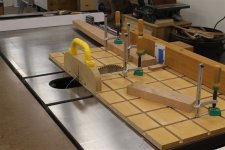
And I end up here.

On to the other parts that make up the end panels.
Last edited: